Fabriquer un acier à faible impact carbone, le défi de la sidérurgie
La sidérurgie est sur le point de transformer durablement son industrie. Le plus grand défi de ce secteur est de parvenir à la fabrication de l'acier avec un minimum d’émission de gaz à effet de serre. Les projets expérimentaux se sont multipliés ces dernières années pour limiter les émissions de CO2 dans l’industrie de la sidérurgie.
A l’heure où le réchauffement climatique se fait de plus en plus présent, l’urgence de l’évolution du climat touche tous les secteurs, y compris l’industrie. Responsable à elle seule de 5 % des émissions de carbone sur la planète, la production de l’acier fait face à un défi historique : s’affranchir des énergies fossiles.
Il s’agit d’un enjeu colossal qui influence nos économies et nos sociétés. L’acier est en effet partout, et notamment présent dans plus de 50% des infrastructures, 14% dans les équipements mécaniques et 12% dans l’industrie automobile. La sidérurgie emploie plus de 6 millions de personnes au niveau mondial.
Fabriquer de l’acier sans CO2, un défi technique
Selon le rapport 2021 de la World Steel Association, pour chaque tonne d’acier produite, une moyenne de 1,85 tonne de CO2 est émise. En 2020, les émissions directes totales étaient de l'ordre de 2,6 milliards de tonnes, représentant entre 7 % et 9 % des émissions mondiales de CO2 anthropique. La Chine produit à elle seule plus de la moitié de l’acier mondial.
Le défi est donc de taille, mais depuis ces dernières années il existe néanmoins plusieurs approches prometteuses qui pourraient être adoptées pour réduire le minerai de fer à l'échelle industrielle, sans rejet de CO2. Ces approches se répartissent en trois grandes catégories :
- L’utilisation du carbone comme réducteur tout en évitant l'émission de CO2 fossile, en faisant appel par exemple à du CCUS (Carbon Capture, Utilization, and Storage en anglais) et/ou de la biomasse durable.
- Substituer l'hydrogène au carbone comme réducteur, générant du H2O (eau) plutôt que du CO2.
- Utilisation de l'énergie électrique par un procédé basé sur l'électrolyse.
Les solutions expérimentées par les industriels
Cette dernière solution est celle qui a par exemple été choisie par AcelorMittal, premier sidérurgiste mondial, après la signature d’un accord d’investissement avec le gouvernement espagnol. Cet accord consiste à construire « la première usine au monde de production à grande échelle d’acier sans la moindre émission de carbone ». Elle devrait fabriquer 1,6 million de tonnes d’ici 2025 à Sestao à 250 kilomètres de Gijón.
D’autres comme la société Mountain Steel au Colorado expérimentent la transition du charbon vers l’énergie solaire, ou encore comme Aço Verde do Brasil qui utilise exclusivement de la biomasse cultivée de manière durable pour sa production d'acier.
De son côté, une start-up américaine appelée Boston Metal, a trouvé un moyen de produire de l'acier en retirant totalement le CO2 de l'équation, pour ne rejeter que de l'oxygène. Ainsi, on ne brûle plus de dérivés du charbon (coke) dans les hauts-fourneaux. Toute la transformation est réalisée dans une cuve par électrolyse, c'est-à-dire en utilisant simplement de l'électricité pour déclencher la réaction chimique.
Industrialiser la technologie propre
L’ultime étape après avoir éprouvé ces méthodes, comme celle de Boston Metal, et montré qu’elles fonctionnent, est de permettre d’industrialiser ces techniques pour fabriquer des pains d’acier propre et solides.
"Notre objectif n'est pas d'en produire directement, explique Adam Rauwerdink, directeur de la stratégie de Boston Metal. Nous voulons nouer des partenariats avec les industriels. Mais avant, il fallait prouver que notre technologie fonctionne, qu'elle est industrialisable et que l'on peut obtenir un matériau de qualité à des coûts raisonnables."
D’autres sidérurgistes suédois SSAB et LKAB travaillent également sur l’industrialisation de ces méthodes avec un projet nommé Hybrit. Leur technique consiste à remplacer le haut-fourneau à charbon par un four électrique et d’utiliser un mélange à base d’hydrogène pour transformer l’acier. Hybrit termine de peaufiner son usine pilote pour passer à la phase industrielle d’ici 2024.
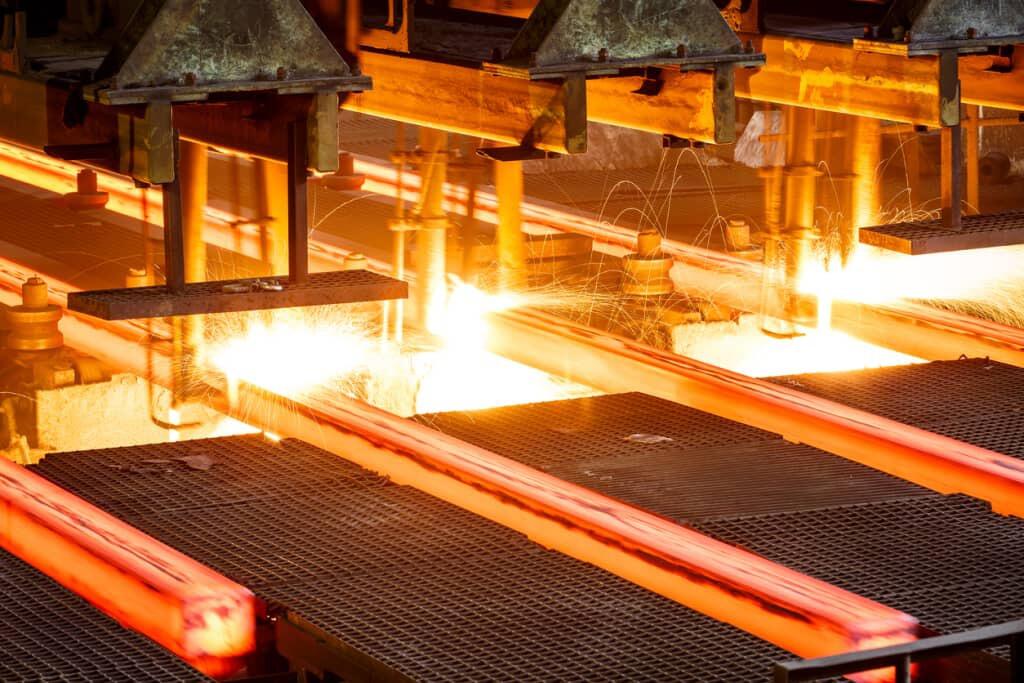